The need for Retro Reflective Devices that could be seen when struck by light at night came about from the introduction of the car into the modern world. From the beginning, automobiles came with lights. However, simply having lights on a dark road was not nearly enough to assure personal safety and prevent serious accidents. In the beginning, when cars traveled slow, it was not as much of an issue. But as vehicles became more popular and much faster, it quickly became important to mark objects such as guardrails, signs, other vehicles, and the road itself so that drivers could safely navigate roads at night. You can see the importance of this by simply driving down a dark road that has no reflective elements. You can quickly see that headlights are not enough, especially if you are traveling at a mile a minute or more.
A brief history outlining the invention, development, and evolution of retro reflective devices and sheeting is outlined below. (Note – Retro Reflectivity is simply the ability of an object to return light back to the source. Also note that reflective and retro reflective are often used synonymous)
Retro Reflective Devices
1906 – Reflectors that bent light and returned it came about from inventors working with lenses and studying their light refracting capabilities. The earliest known patent for a device that was referred to as a reflector was granted to a German inventor named Rudolf Straubel in 1906. He gives evidence of earlier devices in his patent application, where he states that his invention is an improvement of A.Beck’s “triple mirror” system. In his application, Straubel does not specify or make any claims that his invention is for traffic type applications. However, given the development of automobiles at that time, it is probable that he understood the relevance.
1912 – Six years later, a patent was granted to a Robert Venner in the United Kingdom for what he outlined was a method of increasing the night time visibility of signs and word panels. Signs were being used on roads at this point, and the general principle of his invention was to affix glass spheres in grooves or indention’s on the surface of a sign, normally the outer perimeter area, so that it would be visible in one or more directions by light reflected or bounced back from the glass spheres to the light source.
1920’s – Large glass beads that naturally reflect light back to a driver, began to be used to mark words on signs. The stop sign above is an example. So instead of just marking the edge of a sign, this new method marked the actual words. The beads were from 10 – 20 mm in size and quite large. They effectively reflected light back to the source. Light would enter the large beads, reflect off the backside, and return in a parallel but opposite direction from which it came. In other words, back to the source of the light. Around this same period, large cube corner reflectors made of glass were also experimented with. Like glass beads, these cube corner reflectors returned light to the source.

1927 – Seven years later, an inventor from the United Kingdom named Percy Shaw patented a device he described as Cats Eyes or Cataphote Reflectors. This was a great improvement over the glass spheres placed in grooves on the edges or words of signs. Much like a diamond ring, cataphotes were glass beads placed in a setting. This allowed the manufacturer to control the performance of the reflector, which resulted in better photometrics. Also, the device or setting that held the large bead made it possible to attach cataphotes to a variety of surfaces. Mr. Shaw’s invention became very popular and was quickly integrated into road markers, signage, and guard rails. As an example of their importance, during World War II, when automobiles had to operate with low lights during blackouts, cat’s eye (Cataphote) reflectors proved to be very valuable at helping automobiles navigate in low light conditions. Other reflectors also existed at the time, such as plastic and glass cube corner reflectors. However, the Cataphote reflector or Cats Eye outperformed all of these devices in both reflectivity and durability. Note – Percy Shaw is also credited with the invention of the road marker or road stud which is the reflector that attaches to the road itself.

1928 – Jonathan Cass Stimson, a United States inventor, creates and files for a patent on his cube corner reflector array. If you look at the original drawings in his patent, you can clearly see that his triple mirror cubed corner prism is the same array used to this very day for a multitude of reflective products. The reflectors were originally made with glass and then transitioned to plastic, most likely because of ease of manufacture and cost. After filing for his patent, he formed a company called Stimsonite. A name that to this day is very well known in the traffic safety industry. Stimsonite retro reflectors were widely used on automobile tail lights, highway signs, guardrails, railroad signals, airport runways, marine navigational markers, bicycles, and more. Stimsonite is also credited with the invention of the modern cubed corner raised pavement markers that we see on roads today. (picture below) These markers are still manufactured by Stimsonite, and still used on roads today. Note – decades after their original invention and patent, Stimsonite would be the second company in the US to develop prismatic sign sheeting. This invention integrated the prismatic array into a flexible adhesive backed film.
Early 1930’s – Large glass beads already existed. However, in the 30’s, Potters Beads began creating perfectly round, high clarity glass spheres that were a fraction of a millimeter in diameter. Micro spheres. Like the larger beads, when a beam of light entered the tiny glass sphere, it would change direction as it entered, bounce off the backside of the bead, and then bend one more time as it made its way back out of the bead and to the light source. It would do this no matter which direction the light came in from, and if multiple sources of light were shined on the beads, the spheres would return light back to each source. Microscopic glass beads that reflected light opened up several invention opportunities. All of which changed the world of night time visibility.

The tiny beads that Potters Beads created were initially used to light up cinema screens and were later used to add to the surface of painted lines on roadways so that the lines would reflect car headlights and light up a bright white at night. To this day, Potters Beads continues to be the world’s largest producer of micro glass beads and their reflective beads are still used for highway lines and in airports (picture above) all over the world.
Retro Reflective Tapes
1937 – 3m develops a way to integrate micro reflective beads into a pliable, thin, self adhesive material. Minnesota Mining and Manufacturing or 3m hoped to use the film to create stripes on streets and highways, however, because of issues with longevity and adhesion, they changed from trying to create road striping, to trying to make signs reflective at night with a similar film. The beads in their experimental new film were initially exposed. This provided good reflectivity, but when it rained and the surface became wet, the beads stopped reflecting. This was a problem, since low light visibility in the rain was paramount. 3m solved this issue by coating the exposed beads with a clear polymer to protect them. The idea worked, and although reflectivity was reduced by the layer, the film would now reflect in the rain, and would be somewhat self cleaning. When colored tint was added to the clear polymer, the tapes reflected the color of the tint. This is how different colored reflective tapes were created. (Of note is the fact that later, 3m actually did create a road striping tape with their Stamark line of road marking products.)
From 1937 – 1947 3m’s new product, which they called Engineering Grade (Type 1) was further developed and improved. At this point in time, engineer grade film consisted of a colored or white top layer, glass beads, a metalized (mirror) backing to give the beads more reflectivity, and an adhesive backing. In 1947, it was brought to market in the UK, and then the US. The new reflective tape or sheeting was quickly accepted and soon almost every sign in the modern world used the company’s new engineer grade sheeting to light the way for drivers. The 3m company would dominate the sign sheeting industry for about 25 years, and as time passed, the engineer grade films they produced were improved through the use of higher index beads and better methods of metallizing the beads so that they reflected better.
1963 – An American company out of Connecticut, Rowland Products (Rowland Brothers) began development of a thin reflective film that used micro prisms instead of beads for reflectivity. If you go back to 1906, you see that triple mirror reflectors were being experimented with. Then, in 1928, Jonathan Stimson patented an array of these reflectors and created products like road markers. These are like the plastic reflectors that you find on your bike, or on stakes in people’s front yards. So it was common knowledge that a cube corner reflector worked and was actually quite a bit more efficient than glass beads. What Rowland Products (later to be called Reflexite) did was combine these small mirrors or prisms with a flexible film. So what 3m did with glass beads and a flexible film, Rowland did with prisms and a flexible film.
As stated above, large cubed corner reflectors like what Stimsonite manufactured already existed, but the Roland Brothers of Connecticut invented a way to miniaturize the prisms and integrate them into a thin flexible film. To accomplish this, man made microscopic prisms, not much larger than a human hair, are embossed (imprinted) onto a clear or tinted polymer, metallized on the back, and then coated with adhesive, which is then covered with a removable release liner. The small prisms in the film, of which there are millions, are much more efficient than glass beads at returning light making this new reflective film over 5 times brighter than engineering grade and double the brightness of 3m’s yet to be launched High Intensity beaded sheeting. Prismatic films are more expensive to make, and more costly to buy, but for applications where viewers need to see the tape from a long distance, this new prismatic sheeting was the perfect solution.

The Rowland Brothers invention would be as big an advancement in reflective technology as 3m’s engineer grade tape was 30 years before and would revolutionize the reflective sheeting industry. In 1970, after patenting their technology, they formed the company Reflexite and in 1973 began marketing their micro-prismatic retro reflective sheeting commercially. To this day, Reflexite (now Orafol) remains a leader in the reflective sheeting industry, with their specialty being vehicle conspicuity, work zone sheeting and personal safety.
1971 – 3m launches a new line of glass bead technology tapes known as High Intensity Type 3 the year after Reflexite (Rowland Products) patented their new prismatic films. This product, also known as encapsulated glass bead sheeting, took glass beads and placed them into honeycomb cells. The beads, instead of being enclosed or surrounded by polymer, were fully exposed beneath a film of very clear plastic with an air layer between the plastic and the beads. This allowed the high index metallized beads to reflect at their highest possible level, about triple the reflectivity of engineer grade. As a comparison, today’s engineer grade films reflect at about 75 candelas while high intensity film reflects at 250. (Prismatic films reflect at up to 1000 candelas) Note – 3m’s original sheeting, engineer grade, was an enclosed lens film meaning that the glass beads were completely surrounded by polymer.
The release of 3m’s high intensity sheeting which used old glass bead technology was an interesting event in that it followed the invention of a much more advanced prismatic film by Reflexite. So an improvement in an old technology was being worked on the entire time that an entirely new way to reflect light with a film was being created. This would be like someone inventing a new horse and buggy, the year after cars were invented. However, since Reflexite did not market their product for signs, 3m’s new high intensity film actually did very well.
1970’s – During the 1970’s Reflexite’s prismatic product gained more and more popularity due to its brightness, its single layer design, and the fact that it could be plotter cut. At the same time, some new players came into the market. Avery Products came out with their own brand of engineer grade films to compete with 3m. In 1975, Seibu, a Japanese company, created a line of glass bead reflective films branded Seibulite and introduced them into the American market. A year later, in 1976, they released the product into United Kingdom markets.
1980’s – Stimsonite, the American company who had patented triple mirror prismatic arrays in 1928, and who was also the manufacturer of the most popular raised reflective road marker in the world, came up with their own prismatic reflective sheeting to compete with Reflexite. This made sense since it was Stimsonite that pioneered prismatic reflectors in the first place. So they basically took their own idea and integrated it into their own branded sheeting. The reflective sheeting they created is actually still around, as you will see below.
1989 – 3m launches their Diamond Grade line of reflective sheeting. This was and is a high quality and very rugged “prismatic” sheeting for signs. Because of their dominance and expertise in the field, their new line quickly became the most popular sheeting for signs. During this time, 3m continued to successfully market their glass bead products for signs and alternate applications and maintained a dominant market share in that product line as well. Bottom line, 3m is very good at marketing their products.
1991 – Seibu is acquired by the Tokyo based company Nippon Carbide. Seibulite reflective films are rebranded as Nikkalite films. Nippon Carbide begins marketing Engineer Grade films, High Intensity Glass Bead Films, and Prismatic Films worldwide and continue to do so to this day. Nippon Carbides Nikkalite brand line of products currently consists of a Type 1 Engineer Grade in both a standard and flexible version (see picture below) , a Type 2 Super Engineer Grade which is twice as bright, a Type 3 High Intensity Grade Glass bead line in both a standard and flexible version, a Type 4 High Intensity Prismatic line, and a Type 8 Crystal Grade Prismatic line. Nippon Carbide’s Nikkalite line is comparable to 3m’s, with both being highly respected in traffic markets around the world.
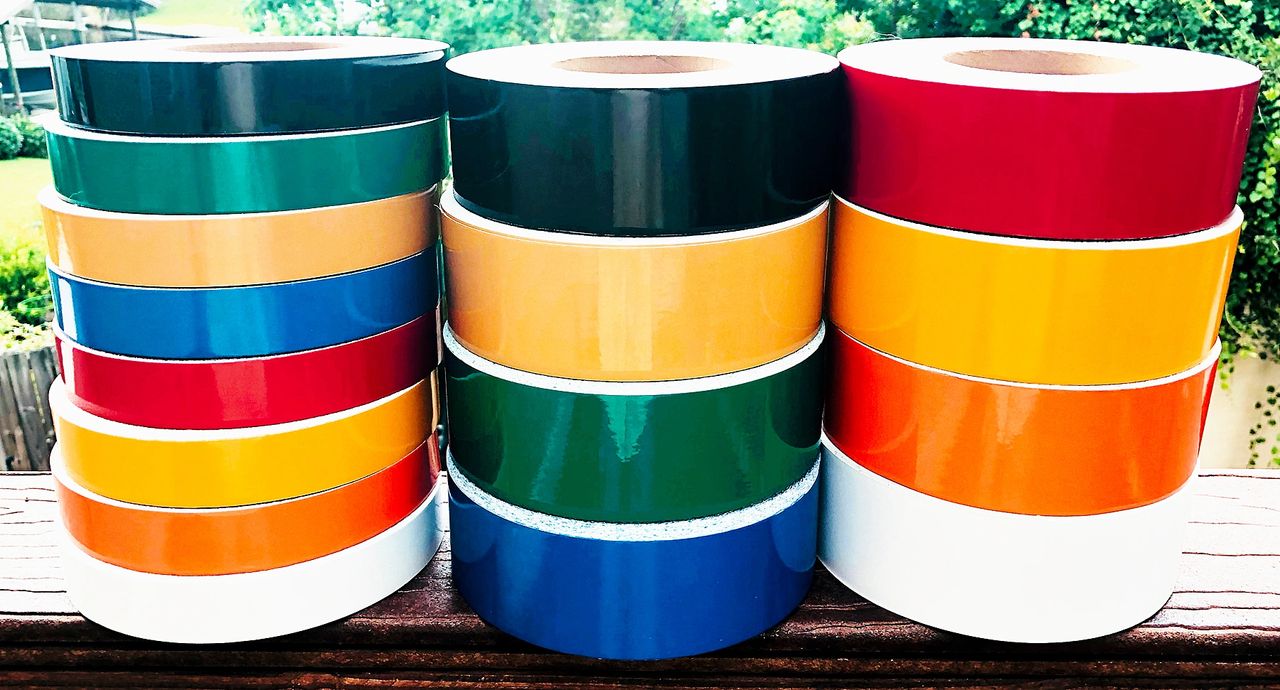
1999 – Avery Dennison acquires Stimsonite and adds the companies micro-prismatic sheeting to their line of retro reflective tapes, thus filling out their product offering. Of note is that Stimsonite is sold again later to Ennis-Flint, but without the reflective sheeting. Ennis-Flint is in the preformed thermoplastic business and buys the company for their road marker line since their two products go hand in hand.
2006 – 3m introduces Diamond Grade DG3 sheeting, which is very similar to their original Diamond Grade, but brighter and reflective at sharper angles.
2006 to present – Companies continue to make improvements to products, modifying prism arrays, making films more flexible for vehicle applications, and offering different adhesives. 3m and Avery’s full cube technology is one example.
Update on Engineer Grade – Due to changes in MUTCD regulations, glass bead sheeting is seldom used for highway signs anymore. However, glass bead films remain very popular for a variety of other applications. A way to look at reflective products is that they never die, they simply have their purpose modified.
In any event, Engineer Grade Type 1 continues to be very popular for graphics applications due to its low price point, wide range of available colors and ability to be easily plotter cut. These features make the film very popular on police cars and emergency vehicles where it is used for striping, letters, and logos. Engineer grade Type 1 films are great for applications where the viewer is close in, say 300 feet or closer. For these applications, brighter, more expensive tapes are often not necessary.
Update on High Intensity Type 3 glass bead tapes. Although not easily plotter cut, high intensity films are still popular due to the affordable price. They are used on bollard, dumpsters, roll off containers, buildings, vehicles, traffic cone collars, and more. They are unique, in that they reflect at wide observation angles. For medium distance applications, Type 3 high intensity is often all that is needed.
Steven Cole (Economics, MBA – University of West Florida , Business & Innovation – Stanford University) 25 years of experience in the reflective safety business. Specializing in vehicle accident and rear end collision reduction through increased visibility.